July 20, 2022
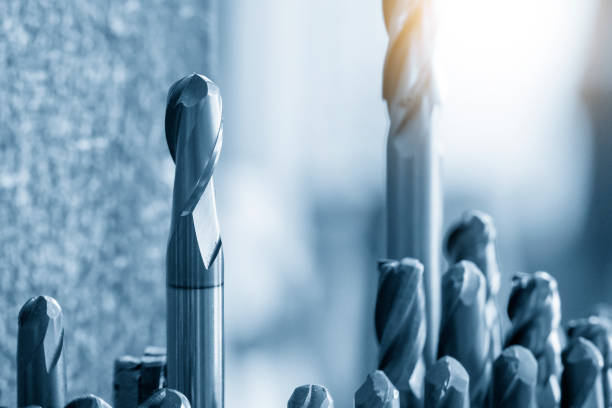
There are five factors that can improve the tool's life and profitability, ensuring fabricators get the most value out of their carbide tools and avoid wear on the tool, and make correct designs
To get the most value out the punching tool, avoid tool wear, and make sure you punch in the correct shapes Take a look at the following five factors.
Correct Adjustment
Fabricators frequently make the biggest mistakes when they do not align their turret station properly and keeping them in good order. This is not limited to their position but also how they are aligned to the punch. If the station is in good alignment, however it is shifted by half a degree, then nibbling or punching out straight lines, for instance with a rectangular tool, will result in a saw-tooth impact every time you make a hit. As time passes the saw-tooth effect will cause uneven wear to the tool, which will eventually break the cutting edge.
Side loading happens when the punch starts to fall, but only a small portion of the tool is in contact with the material. Nibbling can occur through the nibbing. The tool is pulled to the side that isn't supported, which causes the precision tools to degrade.
Experts suggest using a fully guided tool as well as a stripper with a narrower clearance for those who plan to nibble. This will ensure that the precise punch point of the punch is horizontal when it is pierced through the sheet. This is particularly useful for small holes in thick materials as well as nibbling.
Coatings and treatments
Treatments and coatings are excellent ways to increase punch life and reduce the risk of galling. Coating is among the most effective ways to make the most of your tools for punching. A variety of different treatment options and coatings are readily available like a nitride treatment in which nitride is infused into the point of punch.
This makes the punch easier to penetrate the material, and then pull it away. Coatings like zirconium titanium, and nitride are applied in thin, thin layers onto the point of the punch. This adds lubricity to the point of the punch and keeps it cool during high-impact applications where heat buildup can occur.
Proper Die Clearance
The proper clearance is crucial, It has a huge bearing on the stress factor on the tooling, in addition, the finishing of the hole.
Burrs are a sign that your die clearance is not right. A large amount of clearance for the die will result in the material to roll and stretch, resulting in the appearance of a downward-facing edge, or a burr. If the clearance is not strict, this could result in extreme stress on the tool, and the tool may break out of the pierced hole.
When you have the right die clearance, you will get better stripping and a smaller burr. Die clearance is dependent on the material. When using stainless, fabricators normally adjust the clearance of the die up to 25 percent of the thickness of the material. The die clearance for mild steel as well as certain types of aluminum is about 20% less than that of stainless. It all depends on what is being punched.
4.Sharp Tools
A sharp tool can make all the difference to punching hole quality. The most effective way to determine whether your tool should be sharpened is to feel it. If your tool is dull, it will need to be sharpened. You can also determine the shape of the hole if there's an overhang on the edge of the punch this could indicate a dull tool. The tool could be getting worse when the hole is damaged. A circular hole that appears like an egg could indicate that the punch is starting to break down.
It's easy to hear the difference when the punch hits a sheet when it is beginning to become dull. It is advised that fabricators improve their tools frequently instead of punching until they are extremely dull.
It's best to sharpen the tool more frequently and then take a little materials off each time. This can dramatically increase the tool's longevity. For instance, when doing side-by-side testing of identical tools within the same software Sharpening them more often will increase carbide punches the life of tools exponentially.
A good coolant is necessary to sharpen the tool. If you are unable to sharpen with coolant, the heat buildup will alter the nature of the materials, which can weaken the tool. And use a good grinding wheel and constant speeds to feed the tool in and out.
When you've finished sharpening the tool, it's crucial that you demagnetize your tools. As they become magnetic, they attract any carbon-type particles. Any dust or other debris on the tool increases the wear. The tool is basically a way of removing extra garbage.
There could be a scuff around the punch point's edge after tool sharpening. Utilize a soft abrasive remove the material. You'll get a straight edge with a small radius. With dies, after sharpening the die, you should use die shims to ensure they're set to the an appropriate height so that you get the proper punch penetration all the way across the entire board.
Lubrication
Some fabricators will run their punches without lubrication, which could reduce the life of the tool by as much as 60% and cause galling when working on softer materials. The proper lubrication of the tips on your punches can prevent the punch from overheating.
These five tips are essential. You must ensure that your dies and tools progressive punch are stored properly to avoid them rolling around or being scratched.
Posted by: HailieiTorres at
11:14 AM
| No Comments
| Add Comment
Post contains 959 words, total size 6 kb.
32 queries taking 0.057 seconds, 57 records returned.
Powered by Minx 1.1.6c-pink.